Шведский аккумулятор из углеродных волокон произведет революцию в дизайне автомобилей

К концу января 2021 года количество электроавтомобилей в России превысило отметку в 10 тысяч единиц, представленных 18 моделями 14 различных марок. При этом еще в январе 2020 года их количество не превышало 6 тысяч. Несмотря на значительный прирост, Россия еще не входит в топ-25 стран-лидеров по объему продаж электромобилей. Что обусловлено в первую очередь отсутствием на территории России официального представительства крупнейших производителей электрокаров и мировых брендов электромобилей. Также в России слабая мотивационная база, предоставляемая покупателям электромобилей. Поэтому автовладельцы все еще склоняются в пользу приобретения автомобиля с ДВС.
В правительстве уже принимаются меры для того, чтобы автовладельцы пересели на «электрички». Пакет мер для Федерального закона об экологичном транспорте разрабатывается уже несколько лет, при этом, по разным оценкам экспертов, будет принят не ранее 2023 года. Тогда как во многих странах Европейского Союза (ЕС) уже несколько лет существует ряд льгот и преференций для владельцев электрокаров. Но водителей отпугивает не только цена на электромобили, но и страх перед разряженной батареей за сотни, а иногда и тысячи километров от крупного города, в котором еще должна быть заветная зарядная станция, тем более в зимнее время при температурах в ряде регионов 30–40 градусов ниже нуля.
А в течение следующих нескольких лет аккумуляторы, которые будут использоваться в электромобилях, станут настолько дешевыми, что электромобиль будет стоить не больше, чем автомобиль аналогичного размера с двигателем внутреннего сгорания. Но эти электромобили по-прежнему будут весить больше, чем их аналоги с бензиновым двигателем, при этом аккумуляторные батареи в электромобилях составляет 20–25 процентов от общей массы транспортного средства.
Но выход есть: превратить конструктивные элементы автомобиля в сами аккумуляторы.

Батарея из углеродного волокна в виде крышки багажника
Задача
Главный технический директор Volvo Хенрик Грин говорит: «Как наиболее эффективно интегрировать аккумуляторную батарею в автомобиль? Ну, если вы делаете это традиционным способом, вы помещаете батарею в модуль; затем вы помещаете несколько модулей в коробку. Потом вы помещаете коробку в автомобиль, и тогда у вас есть стандартизированное решение, которое можно масштабировать в течение 10 лет.
Но по сути, это довольно неэффективное решение с точки зрения веса, пространства и т.д. Итак, здесь действительно можно пойти глубже, и как бы напрямую интегрировать «клетки в тело» и избавиться от этих модулей, коробок и прочего. Это задача, над которой мы работаем в будущих поколениях автомобилей, и она кардинально изменит их сборку»
.Tesla также работает над разработкой новых аккумуляторных модулей, которые являются структурными элементами, но создает эти структурные модули из традиционных цилиндрических ячеек. Однако есть более элегантный подход к этой идее, и группа из технологического университета Чалмерса в Швеции во главе с профессором Лифом Аспом сделала прорыв в этом отношении.

Демонстрация тестовых батарей из углеродного волокна

Что это и с чем едят?
Наиболее широко углеродное волокно используется в качестве легкого и высокопрочного конструкционного материала в довольно дорогих экзотических автомобилях и самолетах, но постепенно он становится совершенно обычным явлением. Сегодня углеродное волокно используется в велосипедах и клюшках для гольфа, и даже можно приобрести себе бумажник из углеродного волокна.
Выдающиеся свойства углеродного волокна заключаются в том, что в качестве готового материала его можно сделать намного прочнее и легче, чем металлические детали аналогичного размера. Например, углеродное волокно имеет предел прочности на разрыв (то есть сопротивляется растяжению) примерно в четыре раза больше, чем сталь, и в восемь раз больше, чем алюминий. Кроме того, он намного жестче (сопротивляется изгибу), чем сталь или алюминий. При этом такое увеличение прочности сопровождается резким снижением веса: обычно деталь из углеродного волокна весит лишь треть от веса стальной детали того же объема.
Как композитный материал, углеродное волокно получает свою жесткость и легкость благодаря двум вещам: во-первых, это пряди углеродной нити, которая тоньше человеческого волоса, и эпоксидная смола, которая связывает углерод в форму. Второе, что придает композиту прочность, — это химические соединения для объединения двух материалов и последующего их смешивания. Процессы производства углеродного волокна различаются в зависимости от формы деталей, но все методы производства имеют «нить» и «клей».
Конструкция батареи представляет из себя анод из углеродного волокна и катод из алюминиевой фольги, покрытый фосфатом лития и железа, которые разделены стекловолоконным сепаратором в матричном материале структурного электролита батареи. Анод выполняет тройную функцию, удерживая ионы лития, проводя электроны и усиливая все одновременно. Электролит и катод аналогичным образом поддерживают структурные нагрузки и выполняют свою работу по перемещению ионов.

Тесты
Исследователи протестировали различные типы стекловолокна, в результате чего были получены элементы с номинальным напряжением 2,8 В, и достигли лучших результатов с точки зрения производительности батареи с более тонким полотняным переплетением. Элементы, использующие эту конструкцию, имели удельную емкость 8,55 Ач/кг, плотность энергии 23,6 Втч/кг (при 0,05°C), удельную мощность 9,56 Вт/кг (при 3°C) и толщину 0,27 мм. Для сравнения, это 4680 ячеек, которые Тесла помещает в свои машины, чтобы иметь плотность энергии 380 Втч/кг. Однако этот показатель плотности энергии для цилиндрических ячеек не включает массу структурной матрицы, которая их окружает (при использовании в качестве структурных панелей).
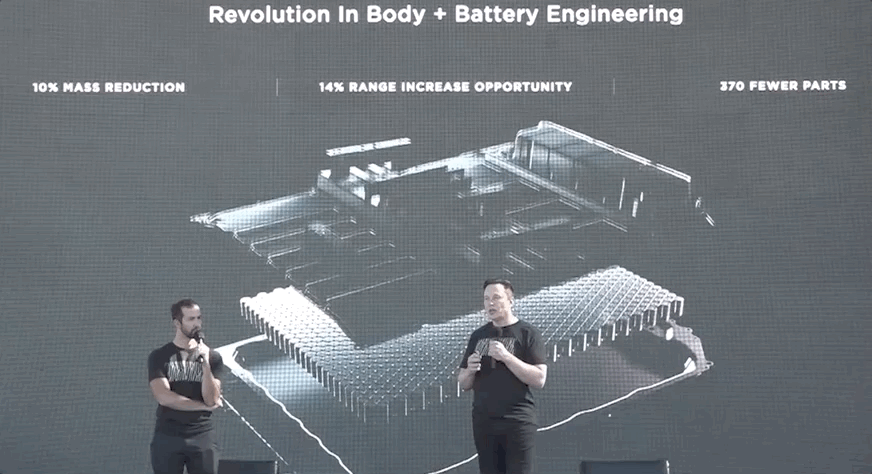

Батарея из углеродного волокна от Tesla
Что касается структурных нагрузок, то наибольшая жесткость была также достигнута при использовании простого стекловолоконного переплетения — 25,5 ГПа. Это примерно похоже на пластик, армированный стекловолокном, тогда как пластик, армированный углеродным волокном, даст результат в 10 раз больше, в зависимости от того, сделан трансферным формованием или является ткаными листами, предварительно пропитанные смолой (известные как pre-preg).
Группа профессора Аспа сейчас работает над тем, чтобы повысить жесткость и электрические характеристики заменой алюминиевой фольги катода на углеродное волокно. Группа также тестирует еще более тонкие сепараторы. Они надеются достичь 75 Втч/кг и 75 ГПа, что приведет к получению элемента, который будет намного жестче, чем алюминий (68 ГПа) и намного легче.

Перспективы
Создание электромобилей или даже самолетов из структурных композитных батарей — пока еще долгосрочный проект, и даже в лучшем случае структурные аккумуляторные элементы могут не скоро приблизиться к характеристикам специализированных элементов, используемых на данный момент. Но поскольку они заменят более тяжелые металлические конструкции, получившийся автомобиль должен стать намного легче, дешевле и экологичнее
Между тем, Асп считает, что преимущества использования такой технологии можно будет увидеть раньше: «Структурная батарея следующего поколения обладает фантастическим потенциалом. Через несколько лет вполне возможно будет производить смартфоны, ноутбуки или электрические велосипеды, которые будут весить вдвое меньше, чем сегодня, и будут в разы компактнее».
На правах рекламы
Наши эпичные серверы — это как Tesla в автомобилестроении. Используем новейшие процессоры от AMD, исключительно быстрые NVMe накопители от Intel и никогда не экономим на железе — только брендовое оборудование и самые современные решения на рынке!